Top Ten Factors to Consider When Choosing a Cast Aluminum Alloy
- zhongshanfuyuan
- Apr 7, 2023
- 3 min read

When it comes to choosing a cast aluminum alloy for your project, there are several factors that are worth considering. Selecting the right alloy has a significant impact on the performance, durability, and cost-effectiveness of your final product. Here are some top factors to consider when choosing cast aluminum alloy:
Application:
The first step in selecting the right cast aluminum alloy is to determine the specific application that your product needs. Different alloys have different properties, which affect their performance in certain applications. For example, if you need a material that has endurance for high temperatures, you should choose an alloy with a higher melting point.
Mechanical Properties:
some of the mechanical properties of an alloy, such as strength, hardness, and ductility, are important to contemplate when selecting a cast aluminum alloy. Different alloys have different strengths and hardnesses, which are directly connected to their ability to withstand stress and deformation.
Corrosion Resistance:
Aluminum is naturally corrosion-resistant, but some alloys have higher corrosion resistance than others. If your product will be exposed to harsh environments, such as saltwater or chemical exposure, it's important to choose an alloy that has high corrosion resistance.
Machinability:
The machinability of an alloy refers to its ability to be easily machined or cut. Some alloys are more difficult to machine and cut, which has detrimental effects on the quality of the product as well as the cost and time required for manufacturing time.
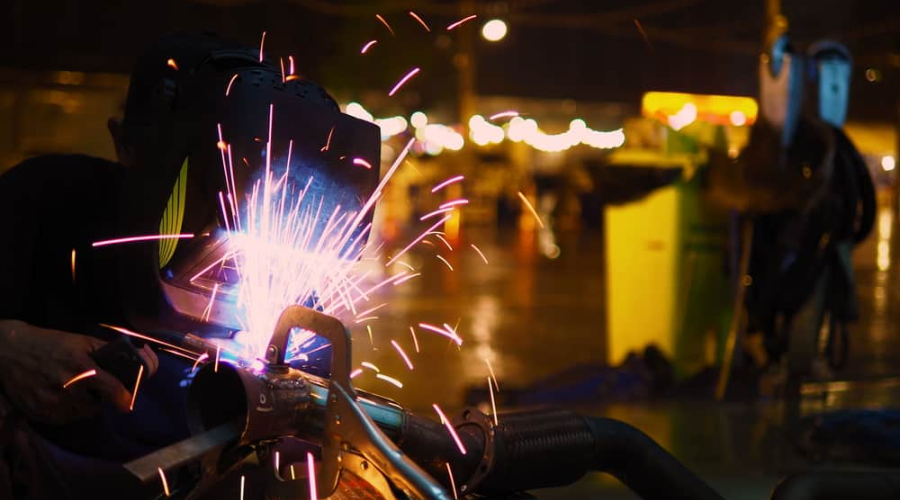
Weldability:
Weldability is a crucial consideration if your product requires welding. Some aluminum alloys have better weldability than other alloys; this property affects the quality and strength of the final product.
Cost:
Cost is always a top consideration when choosing a cast aluminum alloy. Different alloys have different costs, which affects the overall cost of production. It's important to balance the cost of the alloy with its performance and suitability for your application.
Availability:
Some cast aluminum alloys are not easily available in your area; consider the availability of the alloy before making any selection. If you choose an alloy that is not readily available, it will result in increased lead time and cost of production.
Quality Control:
When choosing a cast aluminum alloy, it's important to work with a supplier that has a strong quality control program and certifications. This ensures that the alloy meets industry standards and is free from defects that could affect the performance of the final product.
Supplier Support:
Don't forget to consider the support provided by the cast aluminum alloy supplier. Look for a supplier that offers technical support and assistance, as well as customization options to meet your specific needs. It's also important to choose a supplier who has a good reputation for excellent customer service.
Surface Finish:
The surface finish of a cast aluminum part affects its appearance, durability, and functionality. Different alloys can produce different surface finishes, such as a smooth or textured finish. If the surface finish is critical to your product, it's important to choose an alloy that will achieve the desired finish. Some alloys also require additional post-processing, such as polishing or anodizing, to achieve the desired surface finish. This should also be considered when selecting the appropriate cast aluminum alloy.
Fuyuancasting
Fuyuancasting is a leading manufacturer and exporter of high-quality cast aluminum alloy. All of its products are hailed for durability and seamless finish. Please order with the trusted cast aluminum alloy supplier to get them at affordable wholesale rates
Comentarios