Cutting-Edge Techniques for Casting Complex Copper Parts
- zhongshanfuyuan
- Jun 19, 2023
- 3 min read

Copper is a versatile metal that finds extensive use in various industries. The demand for complex copper parts, both small-scale mini-copper parts and more significant cast copper parts has led to the development of cutting-edge techniques in the casting process. These advanced methods enable manufacturers to produce intricate, high-performance copper components with precision and efficiency. In this article, we will delve into the world of casting complex copper parts and explore the innovative techniques pushing the boundaries of what is possible in copper manufacturing.
Mini Copper Parts: Precision in Small Scale
Mini copper parts play a crucial role in industries that require intricate designs and precise functionality. These small-scale components are used in electronics, telecommunications, medical devices, and more. The casting process for mini copper parts involves specialized techniques to ensure the utmost precision and accuracy. Manufacturers can create mini copper parts with intricate details and tight tolerances by using advanced molds and precise casting parameters.
Cast Copper Parts: Strength and Durability
Cast copper parts, conversely, cater to demanding industries that require robust and durable components. These parts are used in automotive, aerospace, energy, and industrial equipment applications. Casting complex copper parts involves techniques that allow for producing large and intricate components with excellent mechanical properties. Manufacturers can achieve high-density copper parts with exceptional strength and durability by utilizing advanced casting methods.
The Art of Casting Complex Copper Parts
Investment Casting: Preserving Intricacy and Detail
Investment casting, also known as the lost-wax casting method, is a prevalent technique for producing complex copper parts. It includes creating a wax pattern of the desired component, coating it with a ceramic shell, and then melting the wax to leave behind a cavity. Molten copper is poured into the hole, filling the intricate details of the wax pattern. After solidification, the ceramic shell is removed, revealing the finished copper part with exceptional precision and complex features.
Centrifugal Casting: Ensuring Uniformity and Strength
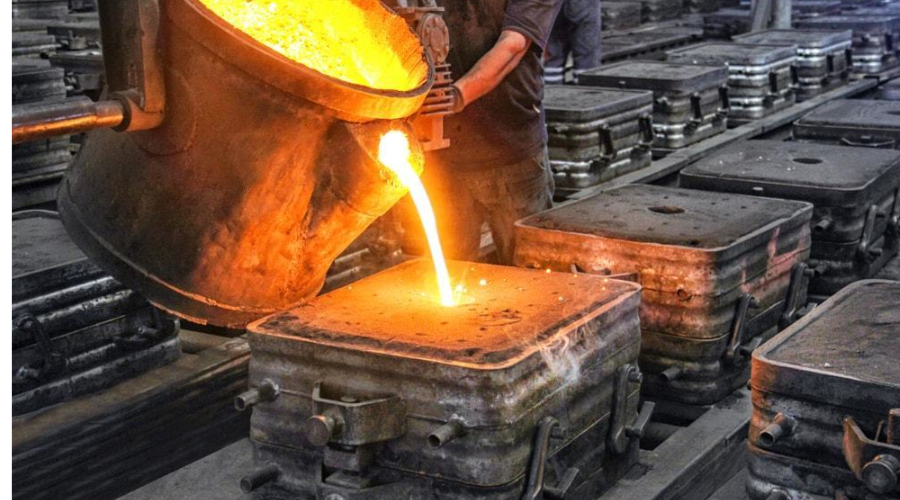
Centrifugal casting is commonly used to manufacture cylindrical or tubular copper parts with complex shapes. In this process, molten copper is poured into a spinning mold, creating a centrifugal force that distributes the metal evenly along the mold walls. The result is a high-quality cast copper part with excellent density, uniformity, and enhanced mechanical properties. Centrifugal casting enables the production of components such as copper tubes, cylinders, and rings used in various industrial applications.
Continuous Casting: Streamlining Efficiency and Consistency
Continuous casting is an advanced method for mass-producing cast copper parts with consistent quality. It involves pouring molten copper into a water-cooled mold, which continuously extracts heat from the metal, causing it to solidify gradually. The solidified copper is then constantly pulled out of the mold, forming a long strand that can be further processed into various shapes and sizes. Continuous casting offers benefits like improved efficiency, reduced production time, and enhanced structural integrity of the copper parts.
Fuyuancasting
Fuyuancasting is a renowned manufacturer and supplier of CNC machines and metal parts. Our products are appreciated nationally and internationally because of their fine quality and seamless finishes. Place your order with a reliable cast copper parts supplier to purchase these excellent cast copper parts at wholesale rates.
FAQs
Q1: What industries benefit from mini copper parts?
A1: Mini copper parts find applications in electronics, telecommunications, medical devices, and other industries that require intricate designs and compact components.
Q2: How are cast copper parts used in the automotive industry?
A2: Cast copper parts are utilized in various automotive applications; engine components, transmission parts, and electrical systems are some examples.
Q3: What are the advantages of using advanced casting techniques for complex copper parts?
A3: Advanced casting techniques enable the production of intricate designs, tight tolerances, excellent mechanical properties, and high-quality surface finishes.
Comments