Cast Iron Machining Tools: Selecting the Right Inserts and Toolholders
- zhongshanfuyuan
- Jun 26, 2023
- 4 min read

When machining cast iron parts, selecting the correct inserts and tool holders is crucial for achieving efficient and accurate results. Cast iron is a notoriously challenging material to machine due to its hardness and brittleness. This blog will delve into the importance of choosing the appropriate inserts and tool holders for machining cast iron bench parts. We will explore different types of inserts, their specific characteristics, and how to match them with suitable tool holders. Understanding these key factorsThis allows you to optimize your machining process and enhance productivity when working with cast iron materials.
Understanding Cast Iron Machining Challenges:
Hardness and Brittle Nature: Cast iron is known for its high hardness and brittleness, making it difficult to machine.
Abrasive Properties: The graphite in cast iron can cause excessive tool wear and chip formation issues.
Heat Generation: Machining cast iron generates heat, increasing the risk of tool failure and dimensional inaccuracies.
II. Types of Inserts for Cast Iron Machining :
CBN Inserts:
Cubic Boron Nitride (CBN) inserts are suitable for high-speed cast iron machining. They offer excellent heat resistance and abrasion resistance.
Ceramic Inserts
They provided exceptional wear resistance, making them suitable for roughing and interrupted cutting in cast iron.
Coated Carbide Inserts:
Coated carbide inserts offered improved wear resistance and reduced cutting forces when machining cast iron.
Polycrystalline Diamond (PCD) Inserts:
PCD inserts excel in high-speed and continuous cast iron machining due to their superior hardness and wear resistance.
III. Selecting the Right Toolholders for Cast Iron Machining
:
Rigid Toolholders:
Opt for tool holders with high rigidity to minimize vibrations and ensure stable cutting performance.
Vibration Damping Toolholders:
Consider using tool holders with built-in damping features to reduce chatter and improve surface finish.
Toolholder Geometry:
Match the tool holder geometry with the insert shape for proper insert clamping and alignment.
Coolant Delivery System:
Choose tool holders with effective coolant delivery systems to dissipate heat and improve chip evacuation during cast iron machining.
IV. Factors to Consider in Tool Selection:
Cutting Speeds and Feeds:
Determining the appropriate cutting speeds and feeds is crucial for achieving optimal results when machining cast iron bench parts. Higher cutting speeds can help reduce tool wear and improve productivity, while meals should be adjusted to achieve the desired chip thickness. Referring to the manufacturer's guidelines and cutting data is essential to establish the correct parameters for the specific insert and tool holder combination.
Depth of Cut:
The depth of cut plays a significant role in cast iron machining. It affects chip formation, cutting forces, and heat generation. Adjusting the depth of cut can help optimize chip control, reduce cutting forces, and enhance the machining process. It is essential to balance the depth of the amount with other cutting parameters to maintain stability and prevent tool breakage or excessive tool wear.
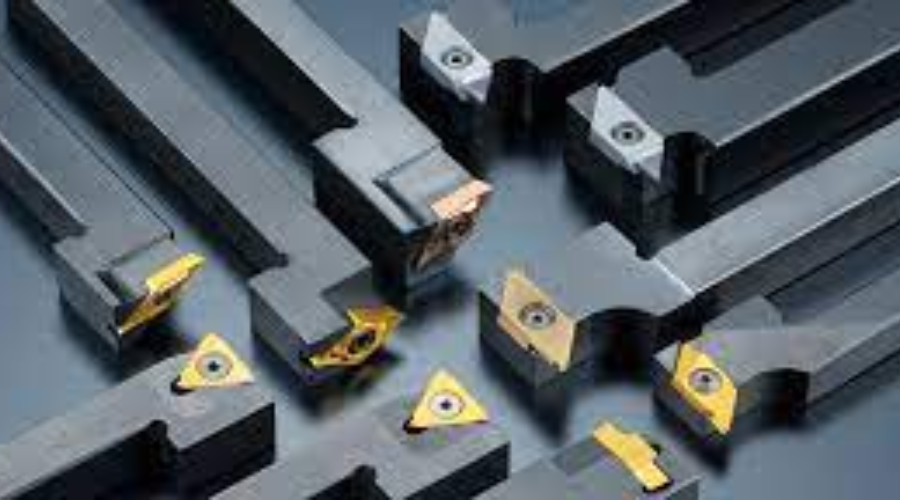
Surface Finish Requirements:
Consider the desired surface finish for your cast iron bench parts. Different inserts and tool holders can yield varying surface finishes. Ceramic inserts, for example, are known for providing a smoother finish, while CBN inserts excel in achieving high-quality finishes in high-speed machining applications. Understanding the surface finish requirements will guide you in selecting the most suitable inserts and tool holders for your specific needs.
Machine Stability and Rigidity:
The stability and rigidity of your machining setup are crucial for successful cast iron machining. Cast iron's hardness and brittleness can lead to vibrations and chatter, affecting the machined parts' surface finish and dimensional accuracy. It is essential to ensure that your machine is maintained correctly, with tight connections, and equipped with robust tool holders that can withstand the forces generated during machining.
Fuyuancasting
Funyuancasting is a renowned manufacturer and supplier of CNC machines and metal parts. Our products are recognized as the best due to their supreme quality and flawless manufacturing. Place your order with the Cast Iron Machining parts manufacturer to purchase these parts at wholesale rates.
FAQs
: Why is selecting the correct insert and tool holder necessary in cast iron machining?
A: The selection of inserts and tool holders directly impacts the machining process and the quality of the final product. Choosing the appropriate inserts and tool holders helps optimize cutting performance, minimize tool wear, reduce vibrations, and improve surface finish in cast iron machining.
Q: What types of inserts are suitable for cast iron machining?
A: There are several types of inserts suitable for cast iron machining, including CBN inserts, ceramic inserts, coated carbide inserts, and PCD inserts. Each class has specific characteristics such as heat resistance, wear resistance, and hardness, making them suitable for different machining applications.
Q: How do I select the right tool holder for cast iron machining?
A: Selecting the right tool holder involves considering factors such as rigidity, vibration-damping features, geometry compatibility with inserts, and coolant delivery systems. Rigid tool holders help minimize vibrations while vibration-damping tool holders reduce chatter. Proper tool holder geometry ensures secure clamping and alignment of the insert, and effective coolant delivery helps dissipate heat and improve chip evacuation.
Q: What factors should I consider when selecting inserts and tool holders for cast iron machining?
A: Factors to consider include cutting speeds and feeds, depth of cut, surface finish requirements, and machine stability. Determining the appropriate cutting speeds and meals based on the insert and tool holder combination is crucial. Adjusting the depth of the cut can optimize chip control and reduce cutting forces. Surface finish requirements guide the selection of inserts and tool holders. Machine stability and rigidity are essential for minimizing vibrations and achieving accurate machining results.
Q: How can I ensure the longevity of inserts and tool holders in cast iron machining?
A: Proper tool maintenance, including regular inspection, reconditioning, and replacement of worn inserts, is essential for prolonging their lifespan. Additionally, using coolant effectively, adhering to recommended cutting parameters, and maintaining machine stability can contribute to the longevity of inserts and tool holders.
Comments