Best Practices for Machining Thin-Walled Cast Iron Components
- zhongshanfuyuan
- Jul 5, 2023
- 3 min read
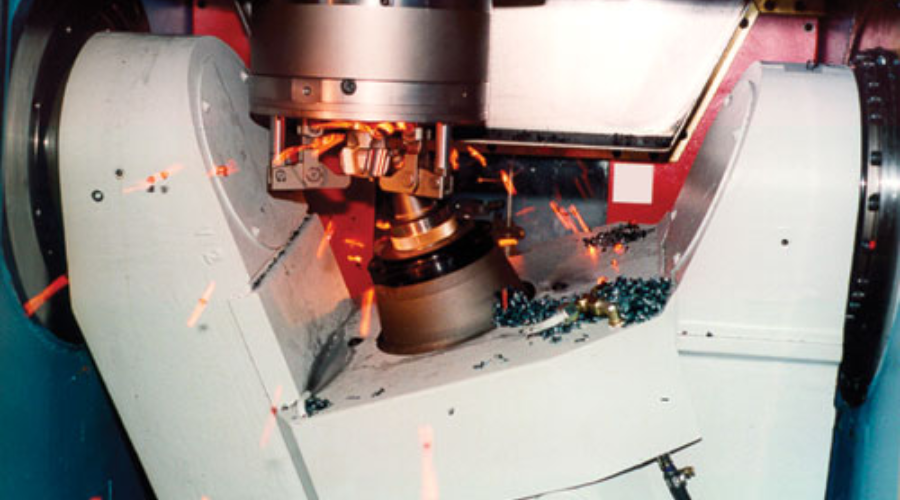
Machining thin-walled cast iron components presents unique challenges due to their delicate nature and susceptibility to distortion and vibration. In this blog, we will learn about the best practices for machining thin-walled cast iron components to ensure dimensional accuracy, surface quality, and structural integrity throughout the machining process.
Understanding the Challenges:
Machining thin-walled cast iron components require careful consideration of the challenges involved. Thin walls are prone to distortion and vibrations caused by cutting forces, leading to dimensional inaccuracies and surface defects. The brittle nature of cast iron makes it more susceptible to tool chatter, chip formation issues, and thermal expansion mismatch. Understanding these challenges is crucial for implementing effective machining strategies.
Machine Selection and Stability:
Selecting the right machine for machining thin-walled cast iron components is essential. Opt for a device with high rigidity and vibration-damping capabilities to minimize tool chatter and vibrations. Stiffness and stability are critical to maintaining dimensional accuracy and surface quality. Ensure proper machine calibration and alignment to reduce errors and deviations during machining.
Cutting Tools and Parameters:
Choosing appropriate cutting tools and optimizing cutting parameters is crucial when machining thin-walled cast iron components. Use tools specifically designed for cast iron machining, featuring sharp cutting edges and suitable coatings for improved wear resistance. Optimize cutting parameters, cutting speed, feed rate, and cut depth to minimize tool vibrations and heat generation. Balancing these parameters ensures efficient chip evacuation, reduced tool wear, and improved surface finish.

Work holding and Fixturing:
Effective work holding and fixturing techniques prevent distortion and maintain dimensional accuracy while machining thin-walled cast iron components. Use soft jaws or custom fixtures to hold the part while minimizing clamping forces securely. Distribute clamping forces evenly to avoid local deformation. Advanced fixturing techniques such as vacuum chucks or magnetic clamps can provide additional support without distorting the thin walls.
Coolant and Lubrication:
Proper coolant and lubrication strategies are essential for machining thin-walled cast iron components. Coolant dissipates heat and reduces friction, preventing thermal damage and tool wear. Consider flood or through-tool coolant delivery to maintain consistent cooling and chip evacuation. Lubrication can further minimize friction and tool wear. Finding the right balance between coolant flow and lubrication is important to ensure the desired surface finish and dimensional accuracy.
Machining Techniques:
Implementing appropriate machining techniques can help minimize vibrations and ensure precise machining of thin-walled cast iron components. Consider using climb instead of conventional milling to reduce tool engagement and vibration. Utilize light cuts and ramping techniques to gradually engage the tool, minimizing sudden forces and reducing the risk of workpiece distortion. Employing adaptive machining strategies can help compensate for any dimensional variations caused by the machining process.
Fuyuancasting
Fuyuancasting is a popular supplier and manufacturer of CNC machines and metal parts. Our top-rated cast iron machining parts are renowned for their premium quality, durability, and seamless finishes. Place your order with the reliable Cast Iron Machining parts manufacturer and get these amazing parts at wholesale rates.
FAQs
What is considered a thin-walled cast iron component in machining?
Thin-walled cast iron components typically refer to parts with walls or sections with a relatively small thickness compared to their dimensions. The specific definition may vary based on the application and industry requirements.
Why is machining thin-walled cast iron challenging?
Machining thin-walled cast iron components presents challenges due to their delicate nature and susceptibility to distortion and vibrations. The thin walls are more prone to deformation during cutting, leading to dimensional inaccuracies. The brittle nature of cast iron also increases the risk of tool chatter, chip formation issues, and thermal expansion mismatch.
How can machine selection impact the machining of thin-walled cast iron components?
Machine selection plays a crucial role in machining thin-walled cast iron components. Opting for a machine with high rigidity, stability, and vibration-damping capabilities helps minimize tool chatter and vibrations that can cause part distortion. A properly calibrated and aligned device reduces errors and deviations during machining.
What cutting tools are suitable for machining thin-walled cast iron components?
When machining thin-walled cast iron components, choosing cutting tools specifically designed for cast iron machining is important. Tools with sharp cutting edges and appropriate coatings for improved wear resistance are preferred. Carbide or ceramic inserts are commonly used for their durability and high cutting speeds.
How can work holding techniques be optimized for machining thin-walled cast iron components?
Effective work-holding techniques prevent distortion and maintain dimensional accuracy in thin-walled cast iron components. Soft jaws or custom fixtures help securely hold the part while minimizing clamping forces. Advanced fixturing methods, such as vacuum chucks or magnetic clamps, can provide additional support without causing deformation.
Comentarios